Welding wire manufacturers like Brookfield play a pivotal role in the welding industry, supplying the essential consumable material that forms the basis of various welding processes. From manufacturing plants to construction sites, the quality and precision of welding wire directly impact the integrity and durability of welded structures.
Welding wire is a consumable material used in various welding processes to join metals. It comes in various forms, including solid wires, flux-cored wires, and metal-cored wires, each designed for specific welding applications and conditions. Welding wire manufacturers are tasked with producing wires that meet stringent industry standards and cater to the diverse needs of welders and industries.
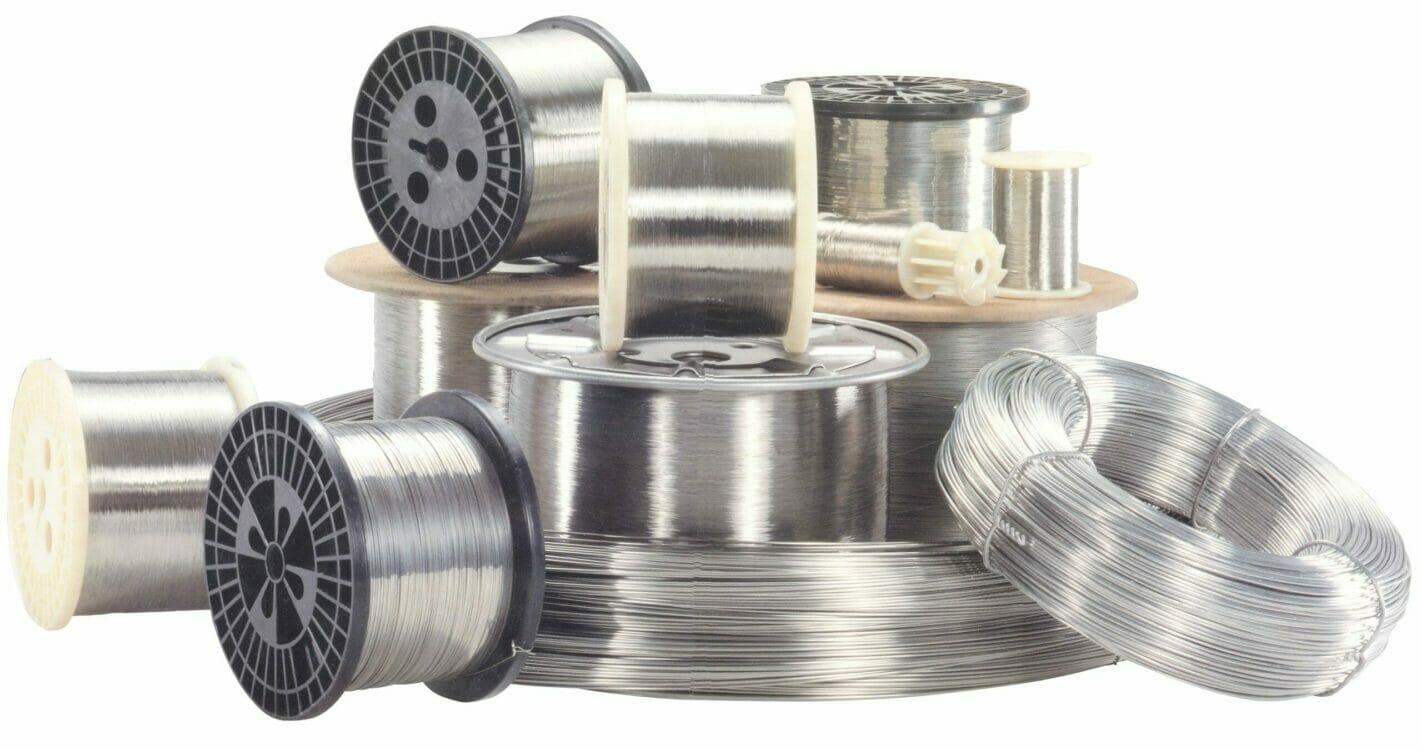
Welding Wire Manufacturer Processes:
Wire Drawing:
The manufacturing journey often begins with wire drawing. High-quality steel rods or coils are drawn through a series of dies to reduce their diameter and achieve the desired wire size. This process enhances the wire’s strength and straightness, laying the foundation for further manufacturing steps.
Wire Coating:
Depending on the type of welding wire being produced, additional coating processes may be employed. Solid wires may undergo processes like copper coating to enhance conductivity and prevent corrosion. Flux-cored wires, on the other hand, involve the application of flux compounds around the wire to shield the weld pool and improve the welding process.
Wire Forming:
The wire is then formed into the desired configuration, depending on the welding process it is intended for. This step is crucial in ensuring that the wire aligns with the specific requirements of welding machines and techniques.
Heat Treatment:
Certain welding wires undergo heat treatment processes to optimize their mechanical properties. This may involve annealing or tempering to achieve the desired hardness, strength, and ductility.
Quality Control in Welding Wire Manufacturing:
Quality control is paramount in welding wire manufacturing, as the integrity of welded joints relies heavily on the consistency and reliability of the wire. Key aspects of quality control in this industry include:
Chemical Composition:

Ensuring that the welding wire’s chemical composition aligns with industry standards is crucial for achieving desired mechanical properties and weld characteristics. This involves rigorous testing and analysis of the raw materials used in wire production.
Diameter and Tolerance:
Precision in diameter is critical, as it directly impacts the stability and uniformity of the welding arc. Tight tolerances are maintained through meticulous monitoring and control measures during the wire drawing process.
Surface Finish:
A smooth and clean surface finish is essential to prevent impurities that could compromise the welding process. Coating processes, such as copper coating for solid wires, contribute to corrosion resistance and overall wire quality.
Mechanical Properties:
Welding wires must exhibit specific mechanical properties, including tensile strength, elongation, and impact resistance. Rigorous testing procedures, such as tensile testing and impact testing, are conducted to verify these properties.
Consistency in Performance:
Welding wire manufacturers conduct regular quality checks to ensure that each batch of wire consistently meets performance standards. This includes testing the wire’s behavior under different welding conditions and environments.
Welding wire manufacturers play a crucial role in ensuring the reliability, quality, and innovation of welding processes across diverse industries. The precision in manufacturing, rigorous quality control measures, and ongoing innovations contribute to the effectiveness and sustainability of welding practices. As technology advances and industries continue to evolve, welding wire manufacturers will likely play an even more pivotal role in shaping the future of welding, construction, manufacturing, and other sectors dependent on the strength and integrity of welded structures.